Om slitstål
På Partrex är vi noggranna när vi väljer vilka slitstål vi säljer och vad vi rekommenderar till dig som kund utefter det du skall ha stålet till. Vi väger in alla avgörande aspekter utifrån användningsområde när vi väljer slitstål: slitmotstånd, seghet, svetsbarhet och pris.
På marknaden florerar olika varumärken på härdade slitstål men de flesta slitstål som används i skopor, plogar och flak är i Sverige härdade borstål. Exempel på varumärken på härdade borstål är Hardox, Swebor och Bruxite.
Olika producenter kan skilja sig i kvalitet på sina produktionsprocesser och alla tillverkare kan i enskilda batcher misslyckas med stålets kvalitet. Men många tillverkare har idag likvärdigt bra tillverkningsprocesser och jämn kvalitetsnivå. Dock kan de skilja sig åt i hur de justerat sina borstålslegeringar på enskilda produkter och dimensioner med avseende på tex kolhalt i stålet. I synnerhet på grövre stål (+40 mm) skiljer sig också producenterna åt i hur de benämner sina slitstål. Tex så kan slitstål betecknat "500" ha olika egenskaper hos olika tillverkare, egenskaper som bland annat påverkar svetsbarheten. Av tillverkarnas datablad kan man dock utläsa en hel del om stålets svetsbarhet och slitmotstånd.
Gemensamt för alla härdade borstål, oavsett varumärke, är att:
- Ökad hårdhet ger ökat motstånd mot slipande slitage (skopor och plogståls slitage).
- Lägre kolhalt och lägre legeringshalt ger bättre svetsbarhet.
Just det sistnämnda är en avgörande orsak till borstålets stora framgång som slitstål. Med endast 0,0035% bor, tillsatt i stålsmältan på rätt sätt, fås ett relativt låglegerat stål med god svetsbarhet och god härdbarhet till ett rimligt pris. Utan denna fantastiska upptäckt skulle våra skopor, flak och plogstål både vara tyngre och kostsammare. Svenska stålproducenter har dessutom varit pionjärer på borstålsområdet sedan 1970-talet vilket också påverkat svenska entreprenadmaskinredskaps utformning. Idag används borstålslegeringar av stålverk över hela världen.
Partrex säljer slitstålsprodukter särskilt utvecklade och utvalda för svenska skopor, plogar och flak. Fråga oss så hjälper vi er till rätt stålval för just det ni skall använda stålet till.
© Innehållet på denna sida är skyddat av lagen om upphovsrätt. All kopiering utan tillstånd är förbjuden.
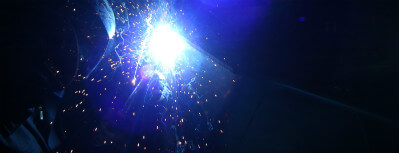
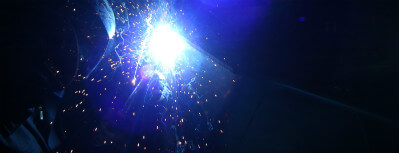
Slitstål som skopstål/skärstål och slitplåt är svårare att svetsa än vanliga svetsbara konstruktionsstål, tex S355. Detta beror på att slitstål har bra härdbarhet. Dina största fiender vid svetsning av slitstål är fukt och för korta övergångar mellan ohärdat och härdat stål vid din svetsfog. Därför är det några saker du skall tänka på när du skall svetsa slitstål som skopstål/skärstål och slitplåt.
Slitståls mekaniska egenskaper förändras mycket vid temperaturförändringar i stålet. Det härdade stålet har mycket hög sträckgräns och låg slagseghet. När samma stål normaliseras (avhärdas) så krymper det något i storlek och får låg sträckgräns. Skillnaden beror på att stålets struktur inuti förändrats från martensit (härdat) till ferrit (ohärdat). Om övergången från martensit till ferrit i slitstålet blir kort så blir det en sprickbenägen “ärrbildning” som kan spricka direkt efter svetsfogen svalnat, några dagar senare eller när den börjar belastas.
Mjuka hårdhetsövergångar vid svetsen - låt värmen sprida sig
Direkt vid själva svetsfogen blir skopstålet eller slitplåten avhärdad och mestadels ferritiskt. För att övergången till ohärdat inte skall bli för för kort så måste värmen från fogen få sprida sig i slitstålet, dvs svetsa inte för snabbt och låt inte stålet kallna för mycket innan du lägger nästa fog. Men tänk samtidigt på att slitstålet förlorar sitt slitmotstånd när det mjuknar så du får inte bränna för hårt heller. Balansen med det är ett hantverk som varje svetsare måste lära sig och det är lite olika för olika slitstålsorter (beroende på kolhalt och legering). En tumregel är dock att stålet ca 7-10 cm från svetsfogen skall ligga på ca 150-200 grader när du svetsar.
För att övergången från avhärdat till härdat skall bli mjuk så får inte det omgivande stålet vara för kallt. Tunnare stål värms snabbt upp av svetsfogen men ju tjockare och större det är desto mer kyler stålet mot svetsen och desto mer kan du behöva förvärma hela stålet innan svetsningen. Tänk också på att stålet snabbt kan svalna under 150 grader, tex när skopan måste vändas så kan stålet behöva förvärmas igen innan fortsatt svetsning.
Hur snabbt slitstålet tappar i hårdhet vid temperaturökningen beror på dess kolhalt och legering men grovt kan man säga att svetsbara slitstål börjar mjukna när de blir över 200 grader. Hårdheten försvinner inte direkt och helt över 200 grader, men uppmjukningen av tex slitstål med 0,27% kolhalt börjar ungefär där och ökar med ökande temperatur och den tid som stålet är över 200 grader. Vid 900 grader är stålet rödglödgat och då är stålet så mjukt det kan bli innan det smälter. Även om minskad hårdhet minskar stålets slitstyrka så bör man i första hand prioritera en mjuk hårdhetsövergång så att man får en stark svetsfog. Minskad slitstyrka på slitstålet runt svetsfogarna är oftast att föredra framför spruckna svetsfogar.
Fukt är svetsens fiende - håll torrt och rent
Din andra fiende vid svetsning, fukt, finns överallt närvarande när du skall svetsa. Fukt, dvs vatten, finns i luften, på stålet, i smuts på stålet och i svetspinnar som legat framme. Vatten består av syre och väte, det är vätet som är stålets fiende. När stålet smälter så dras vätet in i stålet och när stålet stelnar så kan det få stålet att spricka.
Att tänka på för att minimera fukten vid svetsning:
- Förvara svetspinnar i tät och stängd förpackning,
- Gör rent svetsytorna från slagg, färg och glödskal,
- Förvärm skopstålet och slitplåten med gas för att driva bort den fukt som alltid finns på ytan,
- Ha låg luftfuktighet i lokalen, dvs ventilera/vädra (särskilt viktigt om du ofta kör in blöta/snöiga redskap och maskiner i verkstaden).
Slitstål och kolekvivalent
Tillverkare av skopstål och slitplåt anger i regel i sina datablad anvisningar för svetsning av specifika slitstålsorter. Hur stålet reagerar i värme, vilket direkt påverkar svetsbarheten, beror som sagt ovan på dess härdbarhet. Ju högre kolhalt och ju högre halt legeringsämnen ju mer reaktivt i värme är stålet och ju svårare är det att svetsa. Databladen brukar ange ett värde för svetsbarhet, “kolekvivaltenten”, en matematisk formel för att uppskatta stålets svetsbarhet. Ju högre värde på kolekvivalenten ju sämre svetsbarhet. Ju högre kolhalt och ju högre halt legeringsämnen ju högre kolekvivalent. För konstruktionsstål är normen att kolekvivalenten får vara max 0,45. Men ju tjockare stålet är ju lägre bör kolekvivalenten vara för att ha bra svetsegenskaper. Kolekvivalenten är ingen exakt vetenskap och därför förekommer också olika sätta att beräkna den. Dock är det kolet som främst försämrar svetsegenskaperna, legeringsämnena påverkar mindre. Ju hårdare slitstålet är ju mer kol innehåller det i regel och ju djupare det är härdat ju större mängd legeringsämnen innehåller det i regel. “Genomhärdade” slitstål med hög hårdhet är bra för slitmotståndet, men för svetsningen är det försvårande och blir allt svårare med ökande tjocklek. För att maximera både slitmotstånd och svetsbarhet i tjockare stål är det bättre med lägre kolhalt och högre legeringshalt än tvärtom.
Ingen standard för benämningar - titta i databladen
För konstruktionsstål finns standarder och generella benämningar på stålen som betyder samma sak från olika tillverkare. Så är det inte med skopstål och slitplåt. Vad tillverkare kallar sina slitstål och vad de anger om stålets hårdhet är olika mellan tillverkarna, i synnerhet i tjocklekar över ca 35 mm. En del tillverkare har tex mycket höga kolhalter i sina 400 Brinells slitplåtar i grövre dimensioner. Detta för att kunna uppnå hög hårdhet och genomhärdning, men det förstör för svetsbarheten. Samma tillverkare kan också ha slitplåtar benämnda “450” som i samma tjocklek har lägre kolhalt än deras egna “400”. För att jämföra olika tillverkares slitstål gällande svetsbarhet bör man därför titta på kol- och legeringshalterna i databladen.
Val av slitstål
På Partrex är vi noggranna och medvetna när vi väljer skopstål/skärstål och slitplåt som skall svetsas, särskilt i grövre dimensioner. För tex skärstål i 60 mm som man skall svetsa tandhållare i kan en kolhalt om max 0,22% vara ett bra val. Fråga oss gärna för råd om vad som kan vara ett bra val för hur just ni skall använda slitstålet. Gällande val av svetstråd och svetspinnar och rekommenderade förvärmningstemperaturer rekommenderar vi att man utgår ifrån tillverkarens datablad för den aktuella stålsorten.
© Innehållet på denna sida är skyddat av lagen om upphovsrätt. All kopiering utan tillstånd är förbjuden.
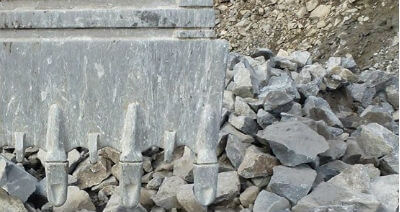
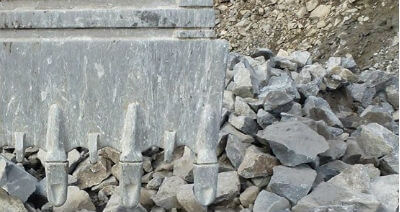
Hårdast vinner. Ett ståls motståndskraft mot det slipande slitage från stenmaterial som skopor, krossar, plogskär och flak utsätts för beror mestadels av stålets hårdhet. När två ytor nöter mot varandra så kommer den sida med det hårdaste materialet att slita ut den andra mer.
Hårda mineraler med vassa strukturer som dras över en stålyta under tryck griper tag i stålets yta och river av den successivt; precis som ett slippapper på en bandputs. Ju hårdare stålytan är ju sämre tag får mineralen och ju långsammare slits stålet.
Den mineral som slitstål oftast slits ner av i Sverige är kvarts. Kvarts är mycket hårdare än det hårdaste härdade svetsbara stål som kan framställas. Granit och gnejs är de bergarter som mest krossas i Sverige och används i vägar och grundläggningar. Dessa bergarter är sammansatta av flera sorters mineraler där kvarts är den största beståndsdelen. Natursand, som fortfarande också utvinns och används i Sverige, innehåller mycket hög halt av kvarts. Dock är natursandkornen slipade mot varandra under årtusenden i vatten så de river inte stålet på samma sätt som krossat material med lika hög kvartshalt. Nivån av kvarts i stenen varierar mycket mellan olika bergtäkter och även inom samma bergtäkter kan det finnas markanta skillnader.
Hur snabbt ett skopstål eller en slitplåt slits ned av tex krossad granit beror till största del generellt av:
- Stålets hårdhet.
- Kvartsinnehållet i graniten.
- Det tryck med vilket stålet och stenmaterialet slits mot varandra.
- Tätheten i kontaktytan mellan stålet och stenmaterialet - finare material - mer kontaktyta - snabbare slitage.
- Friktionsvärmen och stålets förmåga att bibehålla sin hårdhet i den temperatur friktionen värmer upp det till.
I praktiken är det många saker som orsakar faktorerna ovan. Tex:
- Mycket regn ger blöt stenkross som blir tyngre och därmed ökar trycket och därmed ökar slitaget på tex en lastarskopas slitytor.
- Torr väggbana med kallsnö ger hög friktion och dålig kylning och därför snabbare slitage av plogstålen än slask.
- Utformningen på redskapet eller tex skoptanden påverkar hur trycket av stenmaterialet fördelas och därmed slitagehastigheten.
- Hur redskapet körs påverkar slitaget mycket, ibland mest av allt, pga av orsakerna beskrivna ovan.
Hårdhet på stål mäter vi i Sverige oftast med Brinell (HBW). Hårdhet på mineraler anges vanligen i hårdhetsskalan Mohs. Mohs skala är 1 till 10 där 10 är hårdast. Hårdaste mineralen är diamant (10). Kvarts ligger på 7 Mohs hårdhet. Hårdast möjliga härdat stål, som har en Brinell-hårdhet på 700 HBW (approx.), motsvarar ca 5,5 Mohs, alltså mjukare än kvartsen. Däremot wolframkarbid (även kallat tungstenkarbid), ligger på 9 i hårdhet på Mohs skala och slits därför mycket långsammare än härdat slitstål vilket tex är mycket användbart i snöplogskär.
Även om inget härdat slitstål är hårdare än den kvartshaltiga sten man bryter eller plogar snö ovanpå så minskar stålets slithastighet med ökande stålhårdhet. I vissa fall kan 50 HBW högre hårdhet fördubbla slittiden på tex ett skärstål på en bergskopa. Ju lägre kvartsnivå det är i stenmaterialet ju mer ökar slittiden för varje brinell. Ju högre kvartsnivån är i krossmaterialet ju mindre skillnad gör varje brinell. I sådana extrema stenmaterial kan tex grävskopans och tändernas design samt maskinförarens teknik ha större betydelse för slittiden på stålet än 25 Brinell mer eller mindre i stålhårdhet.
Friktionsvärme är en ytterligare faktor som dramatiskt kan öka slitaget av stålet. Detta eftersom härdat stål tappar i hårdhet när det nått temperaturgräns. Tex så börjar 500 brinell borlegerat slitstål mjukna vid ca 200 grader. Vanligt 600 brinell borlegerat stål börjar mjukna vid ca 175 grader. Detta blir bla tydligt på plogstål som körs mot asfalt i hög fart. Ju högre fart och press ju högre friktion, ju högre temperatur och därmed mjuknar stålet och det slits mycket snabbt.
Att välja rätt stål är en övervägning mellan olika faktorer. Beroende vad och hur det skall användas. I det beslutet kommer även frågan om svetsbarhet in, läs mer om det här.
Fråga oss om val av slitstål efter just era behov och förutsättningar så hjälper vi er till en bra lösning. Allt beroende på hur slitstålet skall användas.
© Innehållet på denna sida är skyddat av lagen om upphovsrätt. All kopiering utan tillstånd är förbjuden.
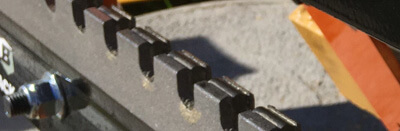
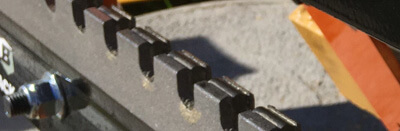
Vad är hårdmetall?
Hårdmetall består av Tungstenkarbid, även kallat Wolframkarbid, som hårdämne och Kobolt som bindemetall. Hårdmetallen är extremt hård, ca 2600 Vickers, många gånger hårdare än det hårdast möjliga härdade slitstål (ca 650 Vickers) och även hårdare än de flesta bergmineraler, inklusive kvarts och porfyr som är mycket vanligt mineral i våra Nordiska vägbanor. Hårdast vinner, är naturlagen i nötande slitage mellan två ytor. På mineralhårdhetsskalan Moh där diamant är hårdast (10), så ligger kvarts och porfyr på 7 Moh och hårdmetallen är ca 9 Moh, alltså hårdare än det hårdaste i vägbanan, vilket ger hårdmetallplogskär mycket lång slitagetid. De hårdaste slitstålen i HBW600 ligger på ca 5,5 Moh, alltså mjukare än materialet i vägbanorna, vilket gör att slitstålet slits snabbt.
Hårdmetall har använts länge inom mekanisk bearbetning, tex i betongborrar. Nu har hårdmetallen även börjat få genomslag inom snöröjningen. Alltfler går över till plogskär med hårdmetall istället för härdade slitstål. Hårdmetallskärens många fördelar ger helt enkelt en bättre ekonomi. Mer kilometer plogning per krona för plogskären, mindre omkostnader på stålbyten och minskad risk för skador på plogen som uppkommer pga genomslitna stål och fel ploginställning till följd av snedslitna stålskär. Sammantaget stora fördelar i en bransch med ständigt pressad ekonomi.
© Innehållet på denna sida är skyddat av lagen om upphovsrätt. All kopiering utan tillstånd är förbjuden.
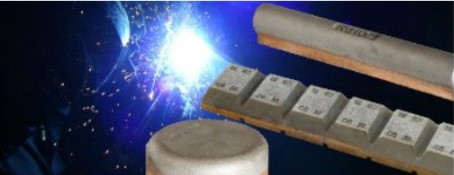
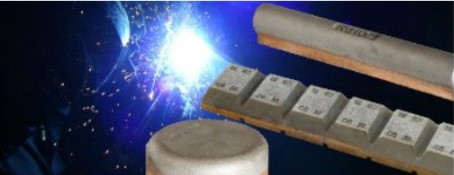
Svetsinstruktion kromkarbid
Bindningen mellan kromkarbiden (grå) och det svetsbara stålet (kopparfärgat) får ej överhettas. Bindningen är en lödning som kan släppa vid överhettning så att
kromkarbiddelen lossnar från den undre svetsbara delen.
1. Placera kromkarbidprodukten så att den hamnar så plant som möjligt mot underlaget.
Chocky bars kan vid behov böjas vid spåranvisningarna för att passa en böjd yta.
Chocky bars kan även delas helt genom att först kapa ståldelen och sedan bryta av eller slå av kromkarbiden med en hammare med mjuk skalle.
2. Rengör ytorna som skall svetsas samman och förvärm lätt med gas för att driva bort fukten från ytorna.
3. Punkta fast kromkarbiden i underlaget.
4. Lägg korta strängar max 50mm åt gången. Byt om vartannat sida för att minimera
risken för överhettning av lödningen i bindningszonen.
5. Lägg inte svets närmare bindningszonen (“bond zone”) än 2mm. Se bild ovan.
VARNING!
ÖVERHETTA INTE KROMKARBIDEN.
FÖR HÖG TEMPERATUR KAN ORSAKA LOSSNING OCH/ELLER SPRICKOR I
KROMKARBIDEN.
© Innehållet på denna sida är skyddat av lagen om upphovsrätt. All kopiering utan tillstånd är förbjuden.
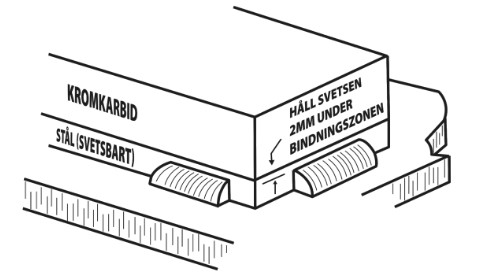
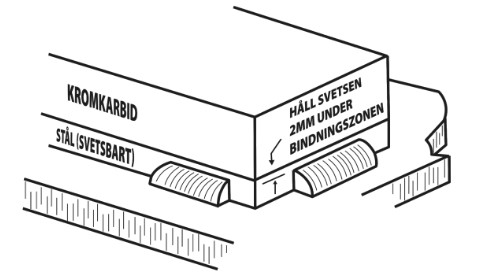